
Z120 Galvanized Coil
Category:
Galvanized Steel Coil
Chat with us now for a quick response.
Get expert sales advice within 12 hours.
Keyword:
Z120 Galvanized Coil
PRODUCT DETAILS
Z120 Galvanized Coil Description
Z120 is the coating name, which means that the coating thickness on both sides is approximately 120g/㎡ or 36g/㎡ (three-point test) and 90g/㎡ (single-point test).
Z120 grade galvanized steel coil is coated with zinc to make it more durable. The working principle of the process is to immerse the coiled steel plate in a galvanizing tank filled with molten zinc. Through the continuous galvanizing process of the thin steel sheet, the galvanized coil is obtained. This type of steel has better formability and good paint adhesion in commercial or architectural use. Another method of producing galvanized steel sheet is through a hot-dip plating process. In this method, it is essential that the steel sheet is heat-treated at 500°C immediately after the exit of the can to form the alloy film coating.
Scope of Application
Galvanizing products are widely used in industry, agriculture, animal husbandry and fishery, energy, transportation, chemical industry, light industry, home appliances, construction, communications, national defense and other fields.
Product Parameters
Product Name |
Z120 Galvanized Coil |
Thickness |
0.12mm-3.5mm |
Width |
600mm-1500mm |
Length |
508mm/610mm, Support Customization |
Standard |
AISI, ASTM, DIN, JIS, GB, JIS, SUS, EN, etc. |
Zinc Layer |
Hot Galvanizing: 60-275g/m² |
Pre-galvanized: 80-275g/m² |
Chemical Composition
Standard |
Grade |
C |
Si |
Mn |
P |
S |
Ti |
Forcold Forming Chinese Standard |
DX51D+Z |
0.12 |
0.50 |
0.60 |
0.100 |
0.045 |
0.30 |
DX52D+Z |
0.12 |
0.50 |
0.60 |
0.100 |
0.045 |
0.30 |
|
DX53D+Z |
0.12 |
0.50 |
0.60 |
0.100 |
0.045 |
0.30 |
|
DX54D+Z |
0.12 |
0.50 |
0.60 |
0.100 |
0.045 |
0.30 |
|
DX56D+Z |
0.12 |
0.50 |
0.60 |
0.100 |
0.045 |
0.30 |
|
DX57D+Z |
0.12 |
0.50 |
0.60 |
0.100 |
0.045 |
0.30 |
|
Forcold Forming Japanese Standard |
SGCC |
0.15 |
0.50 |
0.80 |
0.050 |
0.030 |
0.025 |
SGCD1 |
0.12 |
0.50 |
0.60 |
0.040 |
0.030 |
0.025 |
|
SGCD3 |
0.08 |
0.50 |
0.45 |
0.030 |
0.030 |
0.025 |
|
SGCD4 |
0.06 |
0.50 |
0.45 |
0.030 |
0.030 |
0.025 |
|
For Structure Japanese Standard |
SGC340 |
0.25 |
0.50 |
1.70 |
0.200 |
0.035 |
0.025 |
SGC400 |
0.25 |
0.50 |
1.70 |
0.200 |
0.035 |
0.150 |
|
SGC490 |
0.30 |
0.50 |
2.00 |
0.200 |
0.035 |
0.025 |
|
SGC510 |
0.30 |
0.50 |
2.50 |
0.200 |
0.035 |
0.025 |
|
For Structure AISI Standard |
S220GD+Z |
0.20 |
0.60 |
0.70 |
0.100 |
0.045 |
0.025 |
S250GD+Z |
0.20 |
0.60 |
0.70 |
0.100 |
0.045 |
0.025 |
|
S280GD+Z |
0.20 |
0.60 |
0.70 |
0.100 |
0.045 |
0.025 |
|
S320GD+Z |
0.20 |
0.60 |
0.70 |
0.100 |
0.045 |
0.025 |
|
S350GD+Z |
0.20 |
0.60 |
0.70 |
0.100 |
0.045 |
0.150 |
|
S550GD+Z |
0.20 |
0.60 |
0.70 |
0.100 |
0.045 |
0.150 |
Mechanical Properties
Grade |
Yield Strength MPa≥ |
Tensile Strength MPa≥ |
Elongation A%≥ |
DX51D Z/ZM/AZ/AM |
240-380 |
270-500 |
22 |
DX52D Z/ZM/AZ/AM |
140-300 |
270-420 |
26 |
DX53D Z/ZM/AZ/AM |
140-260 |
270-380 |
30 |
DX54D Z/ZM/AZ/AM |
120-220 |
260-350 |
36 |
S220GD Z/ZM/AM |
220 |
300 |
20 |
S250GD Z/ZM/AZ/AM |
250 |
330 |
19 |
S280GD Z/ZM/AM |
280 |
360 |
18 |
S300GD A/AM |
300 |
380 |
18 |
S320GD Z/ZM/AM |
320 |
390 |
17 |
S350GD Z/ZM/AZ/AM |
350 |
420 |
16 |
S450GD A/AM |
450 |
480 |
15 |
S550GD Z/ZM/AZ/AM |
550 |
550 |
- |
Galvanized Surface Selection
Zero Spangle |
Minimized Spangle |
Normal Spangle |
Large Spangle |
|
|
|
|
Use of The Environment |
Recommended Zinc Thickness |
Indoor Use |
Z10 or Z12 (100g/㎡or 120g/㎡) |
Suburbs |
Z20 and Painting (200g/㎡) |
Urban or Industrial Area |
Z27 (270g/㎡) or G90 (US Standard) and painted |
Coastal Area |
Thicker than Z27 (270g/㎡) or G90 (US Standard) and painted |
Punch or Deep Drawing Application |
Thicker than Z27 (270grams/㎡) or G90 (US Standard) avoid coating peeling after stamping |
Surface Treatment Type |
Code |
Features |
Chromic Acid Treatment |
C |
Good corrosion resistance, suitable for bare state |
Chromic Acid Treatment+Oiling |
S |
Good corrosion resistance |
Phosphoric Acid Treatment (Including Sealing Treatment) |
P |
Have a certain corrosion resistance, good paint performance |
Phosphoric Acid Treatment (Including Sealing Treatment)+Oiling |
Q |
Has a certain corrosion resistance, good paint performance, prevent rust during transportation and storage |
Phosphoric Acid Treatment (Excluding Sealing Treatment) |
T |
Have a certain corrosion resistance, good paint performance |
Phosphoric Acid Treatment (Excluding Sealing Treatment)+Oiling |
V |
Has a certain corrosion resistance, good paint performance, and prevent rust |
Oiling |
O |
Prevent rust during transportation and storage |
No Treatment |
M |
Suitable for immediate painting |
Material Comparison
Chinese Standard |
Japan Standard |
European Standard |
DX51D Z/DC51D Z (CR) |
SGCC |
DX51D Z |
DX52D Z/DC52D Z |
SGCD1 |
DX52D With |
DX53D Z/DC53D Z/DX54D Z/DC54D Z |
SGCD2/SGCD3 |
DX53D Z/DX54D Z |
S220/250/280/320/350/550GD Z |
SGC340/400/440/490/570 |
S220/250/280/320/350GD Z |
DX51D Z/DD51D Z (HR) |
SGHC |
DX51D Z |
Packing And Delivery
Our advantage
experience
Many years of steel experience

01
cooperate
Good cooperative relationship

02
Source
Stable source

03
R&D
Gorgeous R & D strength

04
quality
Reliable quality assurance

05
test
Strict quality test

06
Production





CUSTOMER VISIT
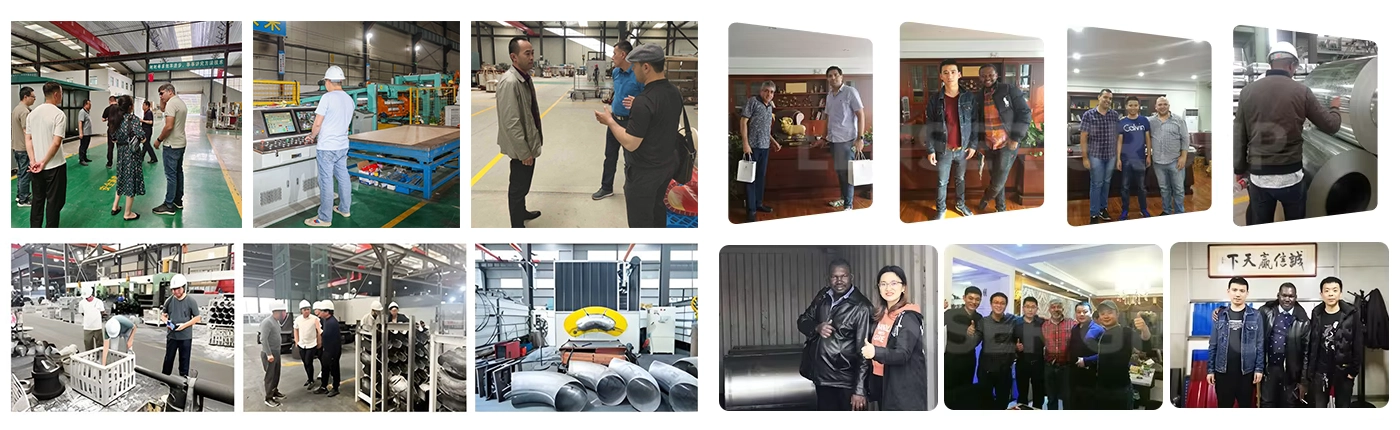
HONOR
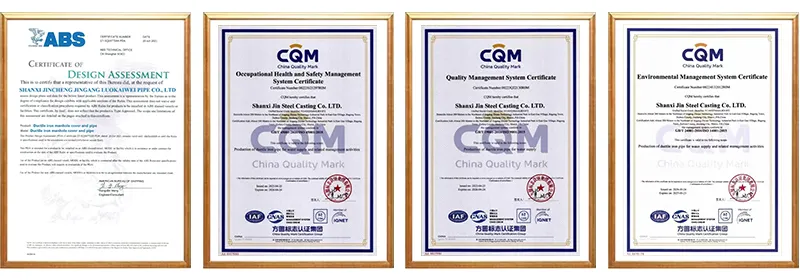

Customer communication

Partner
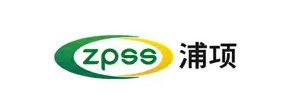
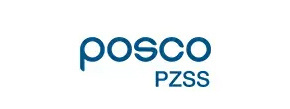
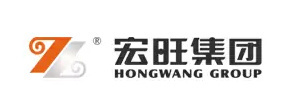
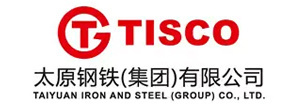
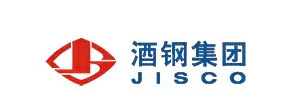
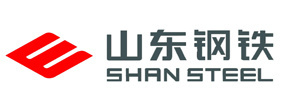
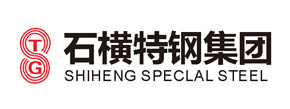
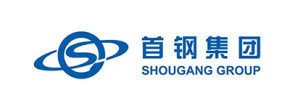
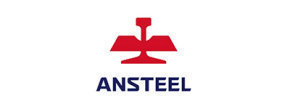
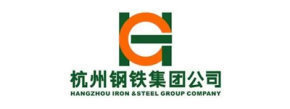
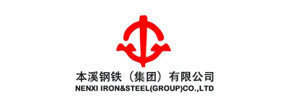
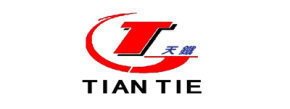
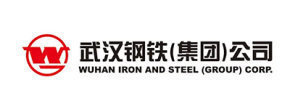
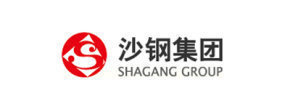
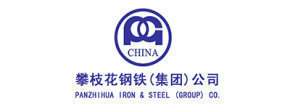
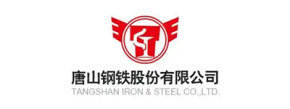
COMMON PROBLEM
FACTORY
APPLICATION SCENARIOS
Oil field
Aircraft manufacturing
Train manufacturing
Ship manufacturing
Power industry
Construction industry
GET A FREE QUOTE
RELATED PRODUCTS